About Bio-based, Biodegradable, Recycled and Compostable plastics
Learn more about Recycled, Biobased, Biodegradable and Compostable plastics
In this article we look closer upon plastic packaging such as Recyclable, Bio-based, Compostable and Biodegradable. In addition, this text is about blades for converting plastic films from these new packaging materials. There is also an article on the blog about cutting specifically PCR plastic here.
Content:
- What are bio-based materials?
- What is biodegradable plastic?
- What are compostable materials?
- What’s the difference between biodegradable and compostable?
- What is recycled plastic materials?
- Examples of recycled, reusable, bio-based, and biodegradable packaging
- So what can you do to get into the Loop?
- Blades for PCR, PIR, compostable, and renewable plastics
Plastics play an important role in modern society, but they also have a significant environmental impact. Reducing plastic impacts while preserving the utility of plastics requires a transition to a more circular and sustainable system for plastic production. The world is changing and flexible packaging manufacturers need to adapt. It puts an enormous pressure on machines and production equipment. The European Commission announced a dedicated policy framework on sourcing, labeling and use of biobased plastics, and the use of biodegradable and compostable plastics.
There are several major changes coming to the packaging industry. In our previous article "Upcoming Plastic Packaging Trends and Regulations" we talked about the upcoming trends and changes in legislation regarding plastic packaging and its place in the circular economy. The conclusion is that legislation and profits pushes the flexible packaging industry towards reusability and recyclability based on renewable and compostable materials.
What are Bio-based Materials?
The term bioplastics covers two different characteristic features of a plastic material. Firstly it is the origin of the input into the plastic production, in this case the bio-refers to biobased. Secondly it relates to degradability characteristics of the plastic at the end-of-life stage; in that case, bio- refers to biodegradability. The term bioplastics is often used inconsistently in the sense that it sometimes describes both characteristics of a material – the material’s natural origin and biodegradability. In most cases biodegradability of plastics refers to industrially compostable plastics.
"Bio-based" is defined in European standard EN 16575:2014 "Bio-based products - Vocabulary" as "derived from biomass". Referring to plastics, “bio-based” is a synonym for the term “made from natural raw materials”. These materials are agricultural products such as corn, tapioca, bamboo, sugarcane, potato or palm leaves; or agricultural waste. Biomass is material of biological origin, excluding material embedded in geological formations and/or fossilized (1, p. 14). Examples are paper and wood, but also plastics such as PLA whose building blocks are produced from sugars.
Bio-based plastics can be engineered to be biodegradable, but its not always the case.
Biodegradability depends on environmental conditions such as temperature, humidity, microorganisms, and oxygen. Biodegradable means capable of being decomposed by bacteria or other living organisms and thereby avoiding pollution (4). Combinations of bio-based and fossil-based resin are commonly used. Anyway, such combinations are referred to as “bio-based”. They may neither be compostable or recyclable (3).
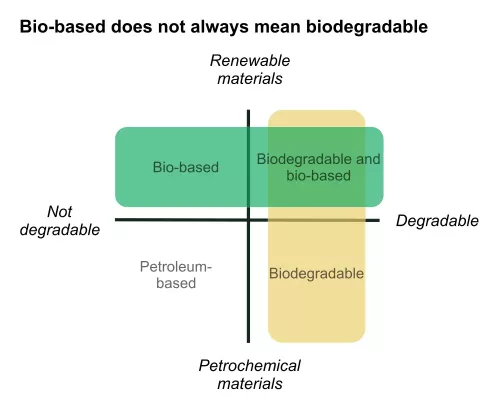
Polymer | Company |
Biodegradable but not bio-based | |
Synthetic polyester | Ecoflex (BASF) |
Polyvinyl alcohol (PVA) | Wanwei |
Biodegradable and bio-based | |
Starch-based materials | Novamont |
Cellulose-base materials | Innovia films |
Polylactides (PLA) | Natureworks |
Polyhydroxyalkanoates (PHA) | Metabolix (ADM) |
Bio-based but nonbiodegradable | |
PDO from bio-based glycerol | Tate and Lyle (DuPont) |
PE from bioethanol | Braskem (Dow) |
PVC from bioethanol | Solvay |
Polyamides (PA) from oils | Arkema |
In Europe, biobased plastics are most frequently used in food packaging (52% or 1.26 Million tonnes of the total biobased plastics market in 2019). They are also used in other sectors, including textiles (10%), consumer goods (10%), automotive (7%), agriculture (7%), coating and adhesives (7%), construction (4%), and others (3%).(5)
What is Biodegradable Plastic?
Biodegradable materials are materials that can be broken down by microorganisms (bacteria or fungi) into water, naturally occurring gases like carbon dioxide (CO2) and methane (CH4) and biomass (e.g. growth of the microorganism population). Biodegradability depends strongly on the environmental conditions: temperature, presence of microorganisms, presence of oxygen and water (1, p. 16). Biodegradable plastic can be produced from both bio-based and fossil materials. Respectively, two types of biodegradability can be distinguished (3):
- Industrially compostable plastics are designed to biodegrade in the conditions of an industrial composting plant or an industrial anaerobic digestion plant with a subsequent composting step
- Home/ambient compostable plastics which are designed to biodegrade in the conditions of a well-managed home composter or in open environments (mainly, this means at lower temperatures than in industrial composting plants)
Biodegradability can be determined using standardized tests that meet the requirements of the European standards DIN EN 13432 and DIN EN 14995 and the US standard ASTM D6400.
What are Compostable Materials?
Compostable materials are materials that decompose under composting conditions. Industrial composting is carried out at a temperature of 55-60°C combined with high relative humidity and the presence of oxygen (1, p.16).
According to the European standard EN 13432:2000 "Packaging - Requirements for packaging recovered by composting and biodegradation - Test scheme and evaluation criteria for final acceptance of packaging" (8), plastic packaging can only be described as suitable for composting if it is proven that:
- The packaging material and its respective organic components (>1 wt%) are naturally biodegradable;
- The decomposition of the packaging material takes place in the composting process of the organic waste within a certain period of time;
- The packaging material does not negatively affect the composting process;
- The packaging material does not negatively affect the quality of the compost.
What’s the Difference Between Biodegradable and Compostable?
All compostable material is biodegradable, but not all biodegradable material is compostable. Biodegradability does not depend on the raw material, but purely on the chemical structure of the polymer. Only some chemical bonds can be broken down biologically, i.e. enzymatically and microbiologically. There are examples of biobased, non-biodegradable plastics as well as examples of fossil-based, biodegradable plastics (3).
Although biodegradable materials return to nature and can disappear completely they sometimes leave behind metal residue, on the other hand, compostable materials create something called humus that is full of nutrients and great for plants. Compostable products are biodegradable, but with an added benefit. That is, when they break down, they release valuable nutrients into the soil, aiding the growth of trees and plants.
What is Recycled Plastic Materials?
Recycled plastic, also called post-consumer recycled plastic or PCR-plastic, can be turned into something new. If the material was made, used, discarded, collected, cleaned, and recycled. If plastic is recyclable, it means it can be recycled in an facility and turned into other plastic products. Post-consumer recycled plastic products short-circuit the plastic product's consumption cycle, allowing them to be recycled into something new instead. Plastic recycling itself is the transformation of used plastic into new products by mechanical or chemical means.
Mechanical recycling involves shredding and melting the plastic waste and turning it into pellets. These pellets are then used as a raw material to make new products. The quality of plastic deteriorates during recycling, so a piece of plastic can only be mechanically recycled a limited number of times before it is no longer usable as a raw material. Therefore, new plastic, or "virgin plastic," is often mixed with recycled plastic.
Chemical recycling covers a set of technologies, such as pyrolysis, gasification, hydrocracking, and depolymerization, that change the chemical structure of plastic waste. The long hydrocarbon chains that make up plastics are broken down into shorter hydrocarbon fractions or monomers using chemical, thermal or catalytic (chemical/thermal) methods. Typically, catalysts and/or very high temperatures are used to break down plastics, and it can be applied to a wider range of plastic waste compared to mechanical recycling. For example, plastic films containing multiple layers or certain contaminants usually cannot be recycled mechanically, but can be recycled chemically.
Read more about Post-Consumer Recycled plastic material in our article "What Is PCR Plastic Packaging And How to Cut PCR"
Examples of Recycled, Reusable, Bio-based, and Biodegradable Packaging
Recycled Plastic Packaging Example
The Swedish plastic film producer Trioworld reduces customers' CO2 footprint by using recycled plastic film. Trioworld has three series of plastics for this purpose: Bio - Biobased plastic, Loop - Recycled plastic, Lean - Reduced plastic. All products containing at least 25% biobased polyethylene are labeled Bio and have a low carbon footprint. Loop is a label for polyethylene film containing up to 80% PCR. Under the Lean label, Trioworld aims to reduce the amount of material used for the application while maintaining or even improving performance.
This producer uses recycled plastics and makes new waste bags with minimum 80% PCR (Post consumer Recycled) plastics. Another example is Trioworld Food Loop 30, which is a laminated film with five layers and 30% PCR which works for frozen food. Some medical Trioworld customers collect all plastic waste and return it to Trioworld that recycles it and makes new medical products of it. Definitely a major step in the right direction.
Reusable Plastic Example
Stora Enso is launching a Bio based material for multiuser packaging. It's more an Ecosystem approach with a joint workshop agreement. Consumers want Easy, Convenient, and Cheap options. It moves food packaging from plastics to Bio-based. Food trays that can be washed 200 times. Tests on this compostable and recycled mono material for bio based food trays are implemented during 2023 in Stockholm, Gothenburg and Gotland.
Among other things, Stora Enso has a range of bio-based material series: FuraCore® by Stora Enso, Lignode® by Stora Enso, MFC for packaging, NeoFiber® by Stora Enso, NeoLigno® by Stora Enso, Papira® by Stora Enso (5).
Bio-Based Plastic Packaging Example
Norwegian food giant Orkla has launched its new sauce bottles in bio-based polypropylene (PP). These bottles contain 90% bio-based PP and are ISCC certified. These bottles show that it is possible to widen the raw material base and to implement the rethinking in packaging on a larger scale. In addition, Orkla launched its first chip packaging using certified renewable polypropylene (PP) from SABIC's TRUCIRCLE™ portfolio. This environmentally friendly material is obtained from tall oil, a residue product of the Nordic forest industry, and converted into BOPP at the IRPLAST plant.
Biodegradable Material for Plastic Packaging
Swedish Gaia Biomaterials have developed a biomaterial called Bidolomer. It is a mineral filled biodegradable material which can be used on existing equipment. Gaia offers Biodolomer granules for a wide range of conversion technologies such as film blowing, injection molding, sheet extrusion, and bottle blowing. As products it means compound, pouches, trays, cutlery, bottles, infills, and bubble wrap.
So What Can You Do to Get into the Loop?
There are basically just three ways forward: reusable packaging, make packaging in compostable or reusable materials, or make renewable materials. In plastic manufacturing it means:
- Use reusable product design
- Collect all your sold products and recycle them
- Use bio-based materials that can be compostable
- Make only mono material plastic products that can be recyclable
Recyclable Product Design
Design is at the beginning of the product life cycle and is necessary to ensure circularity. Product design that is adaptable to the recycling goal facilitates plastic recycling. Design for sustainability and minimize plastic waste. Avoid dark colors and use light colors that will increase recycling value. Ensure packaging is recycled or reused with improved design, e.g. optimize packaging and label compatibility from a recycling perspective, and clearly label which plastic was used in the packaging and tips for sorting or recycling. Label your packaging so it is very easy to recycle. The best product design can generate 77-120 euros for every ton of plastic waste collected. There will be many incentives for manufacturers to get involved in recycling or reuse, which is an interesting business case in itself (2).
Label your packaging in a way that makes it very easy to collect, recycle, and dispose of. Because of the similarity in design, labels on products made of bio-based and/or biodegradable plastic often cannot be easily distinguished from conventional products made of fossil (non-biodegradable) plastic. Logos and labels should be used to make it clear to the consumer whether the plastic is bio-based and/or compostable and, more importantly, how to dispose of the plastic after use.
Packaging from Mono-Materials
Single polymer packaging is easy to sort and recycle, while retaining the original plastic qualities well. Producing plastic film has always been a question of layers and material choices. Using different materials producers have been able to give plastic film variating capabilities. However mixing materials also makes it impossible to recycle.
Borealis and Borouge PLC presented a fully recyclable monomaterial PE laminated pouch. As the company states on its website, еhe entirely mono-material approach to PE eliminates the use of non-recyclable multi-material alternatives. At the same time, it maintains the aesthetic customer attractiveness (look and feel) of the bags as well as their mechanical end-of-life recycling in current flexible PE waste streams (6).
For instance, a bag in just PE that can be collected and recycled to make new products in PE. However, it does require a good way to collect just PE materials without other types of plastics. With clear labeling or marking it is possible to collect separated waste such as PE. With separated plastic waste it is possible to recycle plastics in mono-materials into new plastic raw materials.
Blades for PCR, PIR, Compostable, and Renewable Plastics
It is easy to understand that blades originally designed for cutting virgin petroleum based film will probably not work for slitting plastic film that is recycled, reusable, renewable, or biodegradable.
Cutting PCR, compostable, and renewable plastics clearly changes production settings. Sollex has extensive experience when it comes to blades for slitting PCR (post-consumer) or PIR (post-industrial) recycled plastics. These recycled materials behave similar to multi-layer films and films with printing.
The material texture and abrasive wear is completely different compared to petroleum based materials. That changes the slitting process, which makes it hard for simple blades and circular knives to adapt. High performance or sometimes extreme high performance blades are needed for an adequate slitting process. This is a general recommendation for razor blades on recyclable, compostable, and renewable materials. But each process is unique. Sollex will help you in finding the optimal blade for your process and materials. You can order blades at our shop, email us on info@sollex.se, or give us a call on 0046 35 15 75 00 #1
Sources:
- Van den Oever, Martien & Molenveld, Karin & van der Zee, Maarten & Bos, Harriëtte. (2017). Bio-based and biodegradable plastics – Facts and Figures. Focus on food packaging in the Netherlands. 10.18174/408350.
- Ellen MacArthur Foundation. https://ellenmacarthurfoundation.org/, Accessed the 20th December 2022
- Clara Löw, Siddharth Prakash, Kevin Stuber-Rousselle, Why are biobased and biodegradable plastic not part of the solution to reduce plastic waste?, Oeko-Institut, Germany
- Wikipedia. Biodegradable plastic. https://en.wikipedia.org/wiki/Biodegradable_plastic, Accessed the 20th December 2022
- Stora Enso. Bio-based materials https://www.storaenso.com/en/products/bio-based-materials, Accessed the 20th December 2022
- Borealis and Borouge to present fully recyclable monomaterial pouch solutions at K 2022 https://www.borealisgroup.com/news/borealis-and-borouge-to-present-fully-recyclable-monomaterial-pouch-solutions-at-k-2022, Accessed the 20th December 2022
- Bassas, Monica. (2017). Rediscovering Biopolymers. 10.1007/978-3-319-50436-0_220
- The European Standard EN 13432:2000. Packaging – Requirements for packaging recoverable through composting and biodegradation – Test scheme and evaluation criteria for the final acceptance of packaging
- Trioworld launches recycled food packaging with Lidl Sweden. https://www.mynewsdesk.com/trioworld/pressreleases/trioworld-launches-recycled-food-packaging-with-lidl-sweden-3182181, Accessed the 20th December 2022